A while back, I made a fairly large carving and took some photos that will help guide you through the process when the day finally comes for you and it is no longer a “someday"—it is a “NOW!” There are a few things you should keep in mind. Understand, I’m not telling you not to do it. Far from it! Do it! But to really get the most out of doing it and to actually enjoy the process (which is what this is about, right?), you need to be aware of some things and prepare for them.
Remember that when you make a BIG carving, you need to start out with an even bigger piece of wood. This means that you have to find that big piece of wood, assemble the tools and equipment to actually make this project happen, and do so safely. If you drop an 8" caricature on your foot, it is not a big deal. Mishaps with the log or larger tools are serious! So above all, think safety, and do not try to save money by cutting corners on safety gear or precautionary procedures.
This log came from a ponderosa pine that needed to be removed for the construction of a gymnasium building at a summer camp. It was going to become firewood, but I came along as a volunteer worker with other ideas, which fit with those of the camp administration. The new building was going to be called New Eagle Mountain, so I (along with everyone involved) thought it would be perfect to make an eagle using the wood from this tree.
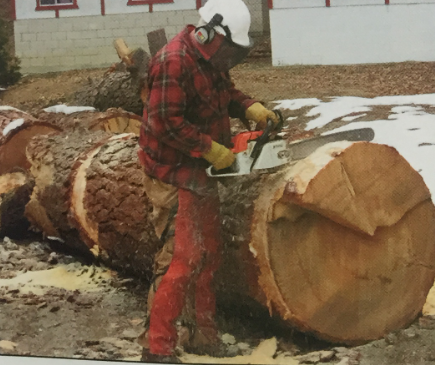
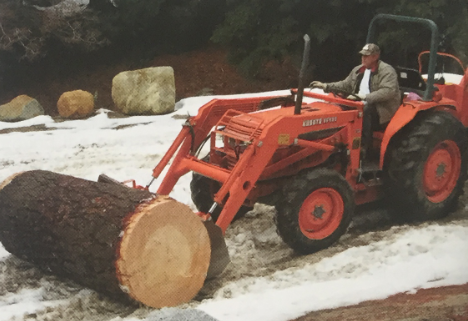
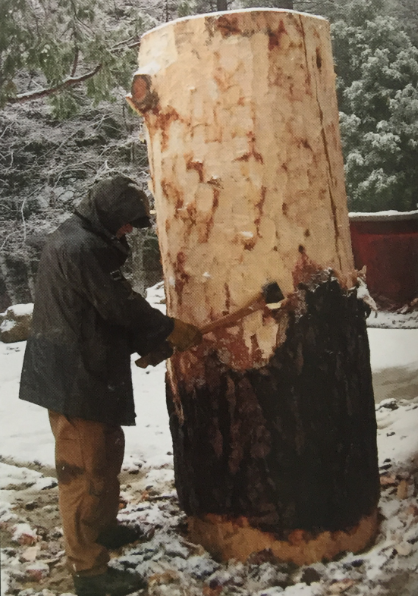
Getting a big piece of wood—a log—can be trie y. Approaching tree removal companies about getting some wood for a project is often a good move. They wi usually be happy that the wood is going to be put to goo use, and may even load the log onto your truck or traier for you. Bring a big enough truck or trailer; wood is heavy. This last fact is why going off into the "boonies to ge a log that has blown down is not so easy, unless you have many willing workers or some kind of machine that can load the log. Getting the machine to the log is expensive—more expensive than going to a sawmill an buying a log. The sawmill workers will load it on the true or trailer free of charge.
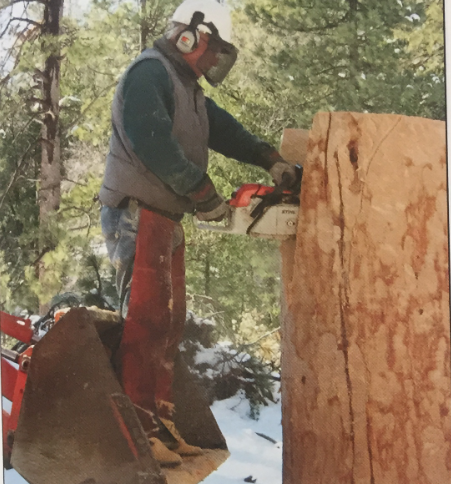
Not only did I have a good log and a good place to work (which is very important, since neighbors can become weary of screaming chain saws fairly quickly), but I also had the safety gear and a few appropriate-size saws. Notice the gear that I am wearing in the photo. Do not start a saw without similar equipment—seriously. You absolutely need ear, face, and head protection (there are special hard hats with a mesh visor and earmuffs that will provide protection for all these areas); wear strong boots and gloves; and do not fail to wear proper protection for your legs in the form of Kevlar chaps or pants.
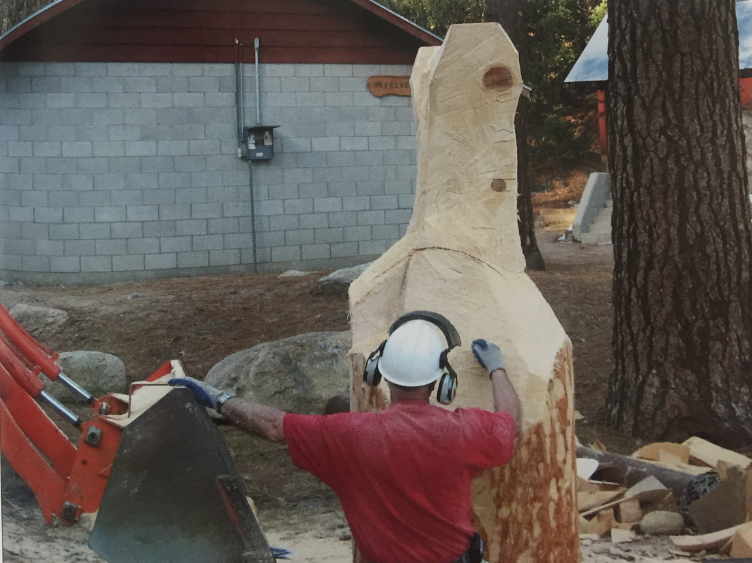
Also get trained—a chain saw can hurt you badly. I know there are chain saw carvers out there who work wearing shorts, a T-shirt, sneakers, and a pair of sunglasses. I think they are nuts. Things can and do go wrong even for well-trained and careful people, and protective gear can save your hide—literally! It has saved mine.
Get a couple of decent saws. One needs to be big enough to do the roughing out; one needs to be light enough to do the carving. Learn to sharpen and maintain them. The air cleaners need to be cleaned frequently— more than once a day. I do not use special carving bars but many carvers do. Special techniques are required for their use.
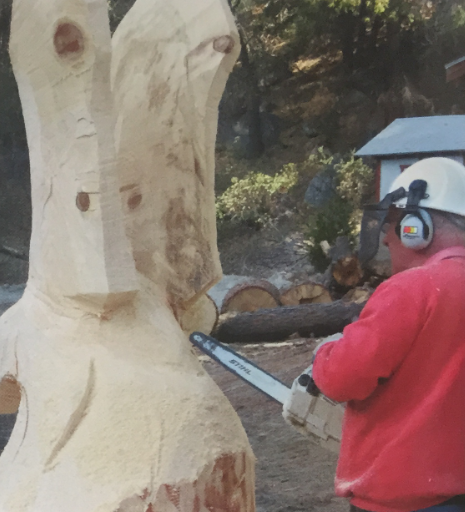
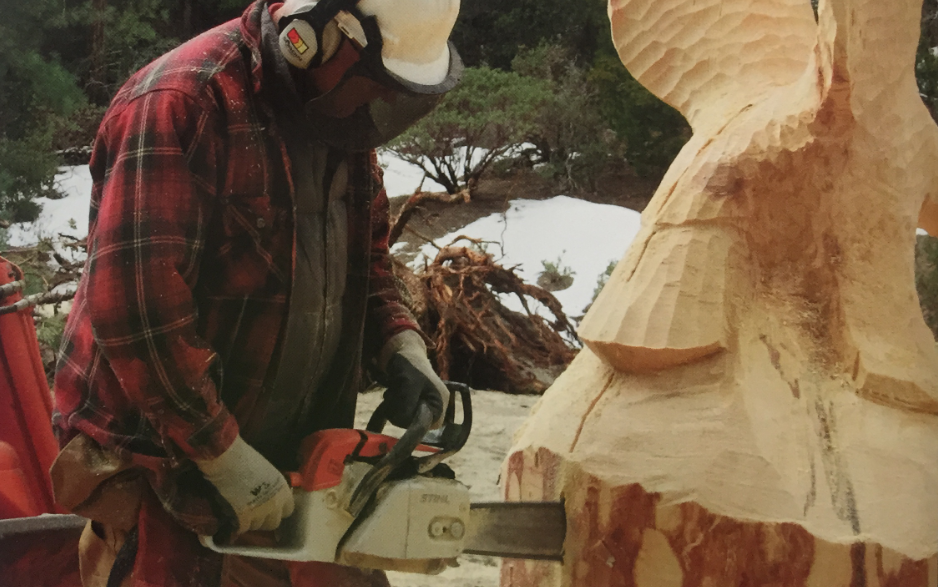
I had a wonderful tractor and a friend who knew how to work it, which made a huge difference. About 10 or 15 strong guys could have done the job too, but I didn't have those. (Two of us tried to roll this log and we couldn’t make it budge.) Make sure that you have not only the wood you need, but also the necessary manpower and transportation required to get the wood to your workplace.
By the way, if you limit yourself to somewhat smaller projects than this one and use logs that can be handled by two or three people, you can get away with using an electric chain saw. This opens up other areas, such as garages and suburban backyards, as workplaces. Just be sure to get the most powerful electric saw that you can and use the safety gear! Electric saws can bite too.
Once the log is in place and stabilized, get all the dirty bark off with an ax. An ax is not very hard to sharpen. A chain saw takes time to file, and the grit that is ALWAYS present on a big log will not only dull that chain but may also chew it up to the point where it won’t be useable at all. I usually wait until I have the log right in position before debarking so that the peeled log won’t get dirty before I get to work on it.
Look at the grit, gravel, and dirt that were in the bark on this log. Touch the running saw to this crud just once and your saw’s chain will be dull.
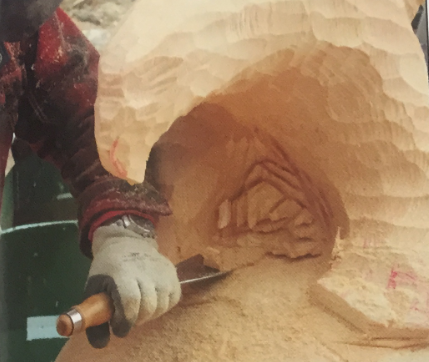
It is absolutely impossible to find a log that doesn’t have grit in the bark. The tree fell on the ground. It has been pushed and dragged on the ground. The ground is almost all grit! Hosing off the bark won’t get the sand off. Use the ax. Trust me. You will save yourself much time and frustration if you take the time to chop all the bark and dirty wood off so that you have nice clean wood to cut with your sharp chain—even if you have to stand out in the snow (in California no less, which just seems wrong!)! Take another look at the picture of me cutting the log to length. Notice that I chopped off the bark all around the log where I was going to saw it. No, you can’t saw grit even a little. One touch and you need to file.
I have belabored the grit removal topic somewhat, but I have been involved in competitions where I was chopping while the other guys were sawing furiously. After awhile, they were filing and I was really making the chips fly, and I didn’t have to file my saw every 30 minutes. If you don’t saw grit, then you don’t have to file your saw very often. Sharp tools make for happy carving.
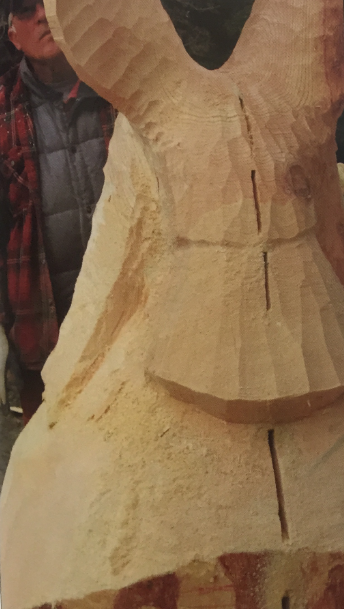
Solid footing and stable scaffolding are essential for comfort and safety. Falling off a rickety ladder while holding a screaming chain saw can ruin your day.
Have your subject firmly in mind and reference materials (photos, drawings, or a smaller model) handy so that you can boldly rough out the log with your big saw. If this is your first large project and it is a subject that you have not done before, I strongly suggest that you carve a model out of a little “log" first so that you will know where to cut boldly and without regret (!) on your big log.
Stop and draw often. A timber crayon or a felt pen is very inexpensive, and can really help you stay on track. Don't make elaborate drawings on the log. If you do, you will be reluctant to cut them off (not cutting off drawings on carvings will lead to square carvings). Do not make square carvings! Animals, birds, and people are not square, and they generally do not have straight or parallel (or both) elements (if they do, they have very few). Step back and take a look at your drawings from time to time. If you see straight lines, something is wrong. Cut your lines off without fear or regret, redraw, and avoid squareness!
Rough out the entire carving; then go over it again and again, getting closer and closer to the finished product. Switch to a smaller saw as the detail gets finer and the amount removed with each cut gets smaller. The smaller saw will be much easier to control and will tire you less.
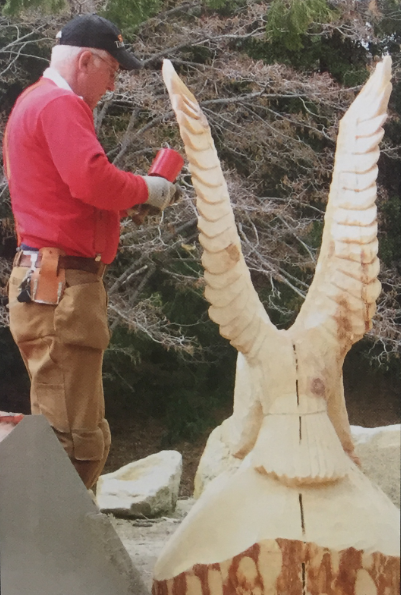
When the basic shape has been achieved, I use the big saw and do a series of plunge cuts that go right into the center of the log in a line right up the back of the carving. This creates a weak spot in the log so that when the log dries and shrinks, the resulting check (crack) will be in the place that will detract the least from the finished product. It is not possible to stop the cracking. Try to direct it instead.
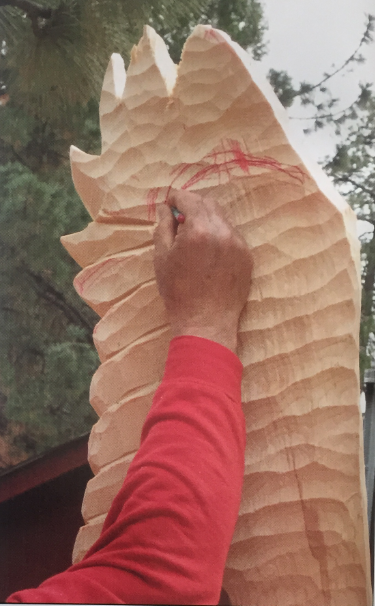
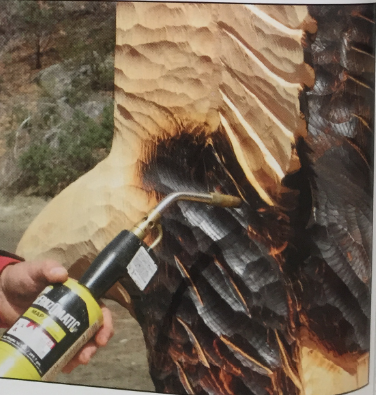
Caution! Learn to plunge-cut safely. Kickback can occur here and it can be deadly! Keep your head and face away from the line of the chain so that if kickback does take place, the saw will kick over your shoulder and not into your face.
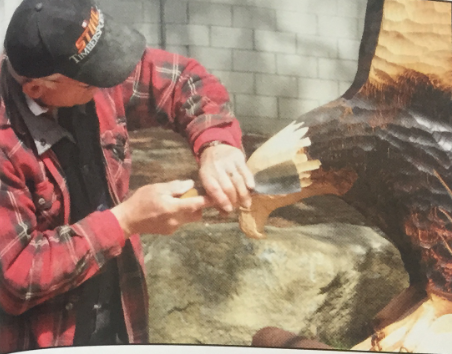
Decide on finishing tools: you may choose power tools (such as angle grinders or special carving bars with tiny tips for your saw) or various die grinders. I have found that a mallet and gouges are just as fast, much safer, need no electricity or gasoline, and produce a wonderful effect. I like to remove all traces of chain saw marks with gouges and do the entire final detail with sharp-edged tools. If you're going to carve, you have to learn how to sharpen your tools. This is true for gouges, chain saws, and knives, Accept it, learn it, and revel in the joy of clean cuts.
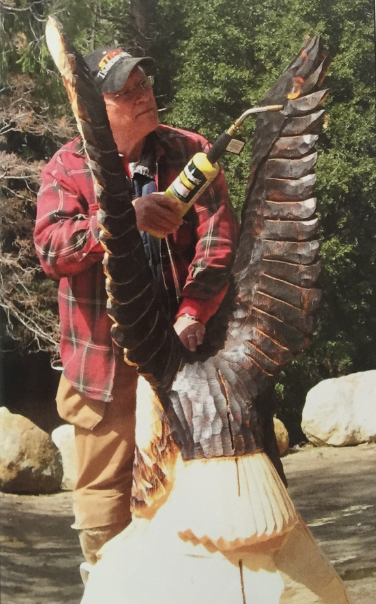
Large V-toois and veiners can produce detail that is crisper than any chain saw or angle grinder can produce. A #7-60mm gouge can remove a great deal of wood in a short amount of time.
In timed competitions, I have found that I can work just as fast with sharp hand tools as those who are working with power tools to finish and detail their carvings. At this point,
I am usually ready for a bit of peace and quiet anyway— that and the opportunity to emerge from under the hard hat and other confining gear.
For color, I resorted to—I admit it—using a torch, although some carvings do better with paint. But please, please do not slap on thick paint and make your carving look like a plastic or plaster casting. It is wood. It should look like wood. No one should be in any doubt that it is wood. (In other words, be easy on the paint, and if you do use it, thin it brutally!)
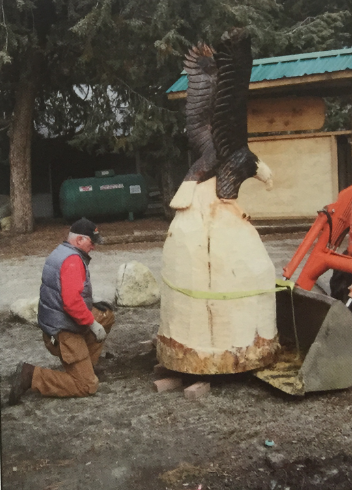
At some point, the project will be done! It may surprise you when this moment comes. (Notice the 8" deep sawdust and scraps. Somebody has to clean this up.)
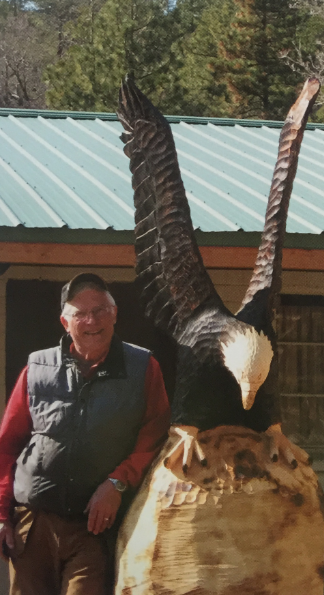
That tractor was very useful in moving the carving to its display location, even though the log had lost a great deal of weight. Be careful in that final move. And when you put that big carving in place, it is best if you do not just sit the piece on the ground. Put it on gravel or bricks or something that will allow drainage. Moisture from the ground can wick up into the log and promote rot. You want this monumental work to last. This eagle lives at Camp Maranatha in Idyllwild, California.
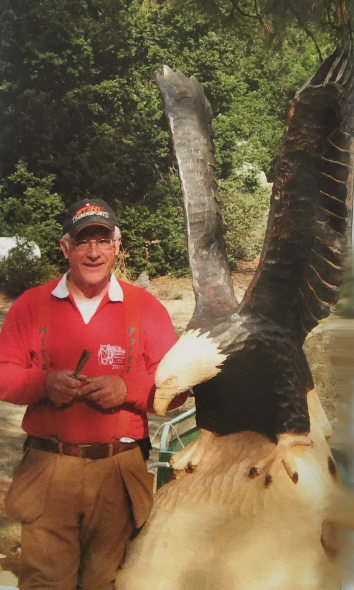
by Rick Wiebe
Rick Wiebe lives in Westbank. British Columbia.